Albuterol shortage sparks VCU study on continuous manufacturing process
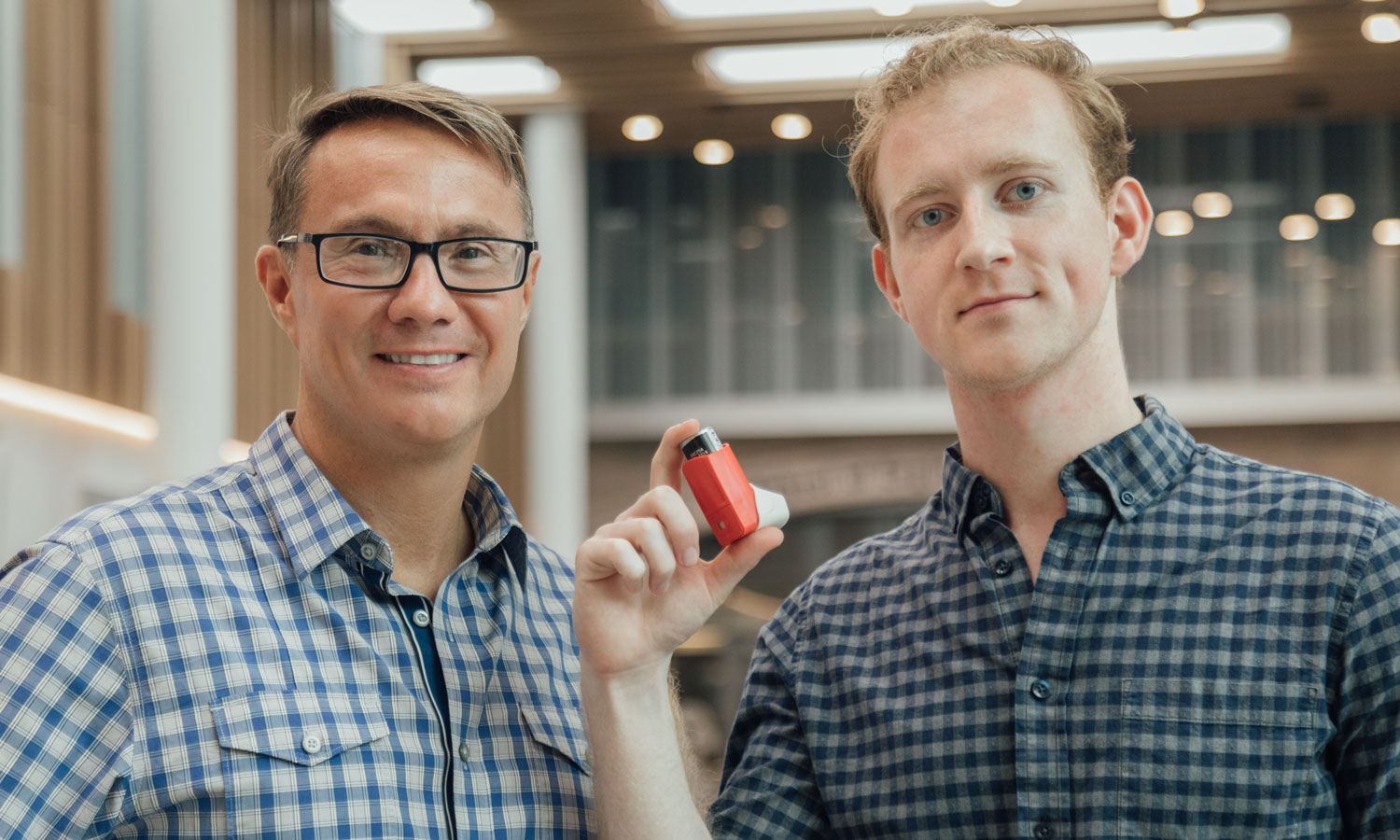
VCU Chemical and Life Science Engineering undergraduate Justin Turnage is amongst a team of students working alongside James Ferri, Ph.D., to identify a more efficient, cost-effective way to produce the common generic drug.
Coughing. Wheezing. Difficulty breathing.
It’s likely that at some point in your life, you or someone you know has used an inhaler to help treat bronchial spasms. Whether for a short term virus like respiratory syncytial virus (RSV) or a chronic disease like asthma, inhalers deliver medicine to the airways, opening the lungs and relaxing the muscles.
The most common generic drug prescribed with inhalers is liquid albuterol. Yet despite its essential status, this drug is one of the latest medications to suffer a shortage in the United States.
This shortage inspired a new research project spearheaded by James Ferri, Ph.D., professor and associate chair in the Department of Chemical and Life Science Engineering (CLSE) at the Virginia Commonwealth University College of Engineering. The project — funded by the US Food & Drug Administration for $5 million and in collaboration with Rutgers University and the National Institute of Pharmaceutical Technology and Education (NIPTE) — looks at how albuterol is manufactured, identifying how chemistry can help build a process that improves efficiency, reduces drug costs and ultimately increases availability for those who depend on the drug.
Mounting Issues with Manufacturing
Supply of liquid albuterol has been steadily decreasing since October 2022 when Akorn Pharmaceuticals, one of the last major albuterol suppliers, stopped shipping its formulation. The generics manufacturer then abruptly shut down operations at three US plants in February 2023.
Three other pharmaceutical companies supply albuterol to the US — Nephron, Mylan and Sun. Only Nephron commented on the shortage, saying they have been unable to meet the demand due to manufacturing issues. Nephron is the only remaining domestic albuterol manufacturer, and though they have since resumed shipping across the US, the climb to normal supply levels continues to be slow.
The result has been limited availability of liquid albuterol and expensive drug alternatives for patients.
Ferri and the research team are examining this problem from two angles: the step-by-step chemical manufacturing process for albuterol and the decentralization of production amongst pharmaceutical companies.
“When there are only one or two big factories making a drug, that is where you run into problems,” said undergraduate Justin Turnage, who joined Ferri’s lab in Fall 2022 and has played a large role in the research thus far. “We’re looking to build a process that increases efficiency and makes it easy to set it up anywhere without specialized infrastructure. That way, if supply chain issues happen, you’re not losing access to the source.”
Chemistry and Continuous Manufacturing
Launched in October 2022, the albuterol manufacturing study will run for 36 months. In addition to Turnage, undergraduate student Brandyn Kimball, graduate students Kaitlyn Kay and Jeffry Noble, senior research associate Daniel Gregory and Frank Gupton, Ph.D., the Floyd D. Gottwald, Jr. Chair in Pharmaceutical Engineering and chair of the Department of Chemical and Life Science Engineering, are also collaborators.
The project is in the early phases of converting chemistry and process steps from batch experiments into continuously running processes. Typical drug manufacturing uses batch processing. This involves multiple steps, and production stops at the end of each step before the process can move forward.
Researchers are looking to develop a continuous manufacturing process for albuterol production, a flow that would eliminate transition times and create the final product much more quickly. Continuous manufacturing has been applied to pharmaceuticals before, but never liquid formations like albuterol.
“The impact of continuous manufacturing methods in improving quality, reducing manufacturing cost and increasing productivity have been extensively demonstrated in a wide range of industries, from automobiles to fine chemicals to food and consumer products,” said Ferri. He first began his chemical engineering career in chemical process development, the first step in translating chemistry to a manufacturing scale. “This project expands the application of advanced manufacturing methods to the second largest category of pharmaceutical products, liquid formulations, including oral liquids, aerosols and liquid injectables. The project will implement and demonstrate a continuous, end-to-end, modular advanced manufacturing system for liquid products.”
“Continuous manufacturing is better at increasing product quality and reducing waste through solvent recycling,” said Turnage. “Traditional batch processes need more space to store solvents, which can be an issue for the manufacturer.”
There are also shelf life constraints when it comes to batch processing. “You may have intermediate chemistry steps that aren’t fully stable and break down over time or over contact with something like oxygen,” said Turnage. “Continuous manufacturing has less interactions with elements like that so there’s less opportunity for breakdown.”
Real World Research, Right Away
Turnage, a senior at VCU, began working in Ferri’s lab during the Fall 2022 semester. He is interested in pursuing graduate school after graduation and knew research was an important part of that process.
“Since joining the lab, I have learned a lot about practical experimental design and how to get the most information out of working with limited resources,” said Turnage. “I have also noticed that my technical communication skills have greatly improved while working on a project with a team.”
Turnage’s participation and lead role on such an impactful, real-world study demonstrates the importance of hands-on research and experiential learning at VCU, both at the undergraduate and graduate levels.
“Undergraduate research is an important part of the enterprise of academic inquiry,” said Ferri. “Undergraduate students who participate in research learn important aspects of critical thinking and problem solving that are difficult to teach in the classroom.”
Projects like Ferri’s allow students to apply theoretical knowledge to practical situations and develop skills essential to a career in engineering. These hands-on research opportunities help students learn to think critically, work in teams and communicate effectively, preparing them for success in graduate school and beyond.
Categories Chemical & Life Science Engineering, Research Grants